In the book The Innovator’s DNA: Mastering the five skills of disruptive innovators, the authors state, “Innovative break-throughs often happen at the intersection of diverse disciplines and fields.” It’s true, there is often merit in taking ideas and innovations from one industry and applying it to one that is unrelated. Travel writer, Giles Foden, has a “cinematic approach” to gain different perspectives in his writing; by varying the lenses through which Foden views the world, he captures the story he wants to tell. On a parallel plain, varying the lens, from wide-lens to zoom may have you seeing your business with fresh perspective.
Carmen Morgan – The Writing on The Wall
I enjoy discovering how things work. And Since I don’t have a job yet, I’ve been spending a lot of time observing business models (mostly retail) and finding a lot of value in looking at them from a “Montessorial perspective”…which is to say, deconstructing their most basic function(s) and then tracing the process backwards from the end of the customer experience back to the production process. It’s how I see my three year old daughter learning mathematics. Her Montessori teachers have broken math down to the core elements of: patience, dexterity, counting and the physical comprehension of quantity
Studying business operations is stimulating largely because of the challenge presented when conventional process systems are often broken to some degree and with a small amount of adjustment…what I like to call: “microfinement of process management”, you can usually find greater efficiency for the multitude of people any single transaction or service affects in it’s lifespan.
The challenging aspect of recognizing curable inefficiencies or identifying potential process improvements is the necessity to view the entire process from an “outside” and “far-sighted” perspective so that every degree of future impact separation can be considered from a distance like a position on a map.
I was going through my closet the other day when it occurred to me that although I was satisfied with the job my dry cleaner was doing with my clothes…all of my shirts seemed to be facing the wrong direction. Instead of the hooks of the hangers making a question mark…they opened to the opposite side (to the right). After trying to relocate the shirts on different bars throughout the closet, I realized that the only fix to this problem was to unbutton every shirt and put them back on the hangers after turning the hanger around so that the hooks of the hangers formed a question mark (opening to the left instead of to the right).
Every article of clothing my drycleaner hung (from my wife’s dresses to my sport jackets) faced the “wrong way”. On our recent move from Philadelphia to Sioux Falls, I had transported a few of shirts and suits that had been dry cleaned in Philadelphia and never came out of the dry cleaning plastic sheaths they were picked-up in. While in the process of pairing shirts up with suits, I noticed that I was able to slide all of the suits still covered in plastic (from my Philadelphia drycleaner) to the right while standing on the left and viewing them from the front. When I placed a recently dry cleaned shirt in front of these particular suits, the shirt was facing away from me and I was unable to view the pairing as it would appear when worn.
Thinking that this may just have been the standard operating procedure of one particular dry cleaner…and being happy with that dry cleaner, I made a mental note to ask them if it would be possible to put my shirts facing in the opposite direction upon my next visit.
It wasn't until several trips later to the dry cleaner that I remembered and had asked if it was possible for them to accommodate my peculiar request. The owner of the dry cleaner informed me that they were unable to change the direction of the hangers since all of the garments go through “a machine” and are all hung in the same direction. I tried to explain why I believed all of the shirts were being put on hangers facing in the wrong direction but I was not successful in effectively communicating my point. I dismissed this minor inconvenience like a man who continues to work with slightly broken tools…until I went to a new dry cleaner out of convenience before a trip out of town. I noticed they too had shirts and dresses hung in a similar fashion. 3 dry cleaners later it occurred to me that most every dry cleaner in town was hanging their shirts and what I had decided was the wrong direction. That should have been sufficient evidence that I was the one whose perspective required some adjustment...but regardless of how hard I tried to accept it, it still bothered me.
I mentioned this to a few friends who dismissed my attention to this minutia of detail as not only silly but also irrelevant and uninteresting. “Seriously?...Who cares?” they said. But my discomfort with this process intrigued me as if it were a puzzle…or a movie title I couldn't remember. I gave it some serious thought and realized that in a world where most of us are right hand dominant and in a country where we read from left to right it would make perfect sense that the clothing industry would display their garments in the manner I expected...in a way that was not only efficient but also enabled a consumer to envision themselves wearing the garments when sliding them left to right (as a mannequin would mirror them).
I went to a few stores ranging from low to high-end (The Salvation Army, Target, Khols, The GAP, Macy’s, J.Crew, Brooks Bothers, Nordstrom, Saks 5th Avenue, Neiman Marcus and Bergdorf Goodman). Every one of these retailers had their garments hung on display racks in the same way. They were all hung so that you can move the items from left to right and quickly observe the shirt, dress, sweater or whatever, on the right hand side facing you as it would be in a mirror if you took the time to try it on. I was discussing this with an executive at Gap North America who told me that she had "spent some time in the fashion industry and explained that it was common knowledge, in retail, that the hanger should always be making a 'question mark' at the top when facing a customer in order to ensure uniformity. Not only on horizontal racks but on rounders [AKA: circular racks) and T-Racks as well. The reason being: so that whether right-handed customers are pulling the garments towards them or pushing the garments away, the garments are always facing the same direction and always 'mirroring' the [right-handed] customer."
What these dry cleaners are doing by putting garments on hangers where the hook goes to the right instead of the left made me question why such a fundamental convenience was not availed to their customers. There was something to learn here in seeing how their system worked. It posed an interesting life-cycle of service opportunity to learn where the breakdown occurred and how I might prevent similar breakdowns in developing production management systems for restaurants… or for any service related business. I went back to my regular dry cleaner that week and told him that I once had an opportunity to work in a dry cleaner one summer as a boy and had always regretted it because of the mystery of what happens to the clothes when they go behind the wall. I told him that I found it very curious and asked if I could take a peek behind the curtain and see the Great and Powerful OZ. He agreed happily and even offered to show me how each station and each machine works. Not surprisingly, the entire process was a horse-shoe shaped assembly line that went from the left side of the store all the way around to the right of the store where the clothes were picked up. The clothes would travel this path of individual stations after being tagged and sorted by hand at the first station.
Some garments go to the laundering station and some skipped to the dry cleaning station (quite a machine!). After being cleaned, some go to the tailoring station while most go to the next station in a large canvas bin with wheels where they are fit over what looks like a large human figure / dummy. (Every dry cleaner has one and so they typically have a name. Theirs was named Suzie) Once the garment is fit over Suzie, the station operator steps on a large metal pedal that emits enough steam from within Suzie to puff out the garment and instantly steam it. After the steaming, some articles go to a long press and some go to a “hand-ironing” station. After each garment is steamed, pressed and or ironed, they are hung on hangers and pinned with a small numbered tag that corresponds to the number on the ticket originally given to the customer when they drop off their clothes. This whole process goes from left to right until the clothes are then bound together in sections with twisty ties and covered in plastic with the customer's receipt stapled to the plastic. The customer then picks up their order, pays and makes haste to their closet where the white noise of clothes hanging in the wrong direction ensues.
After my back stage tour, I explained how it all made sense to me why the garments were hung the direction they were on the hangers. I explained to the owner that it all made sense to me now and that I understood the garments are hung on the hangers the way they are because the assembly line moved from left to right and you always have the next station in the line receiving the garment from the left and facing them head-on….as is necessary. He smiled upon my “seeing the light” with an almost perceptible sense of satisfaction. I thanked him very much for my tour and left. What I didn’t share with him was that the problem with this process is that it values the employees’ need to see the garments in a convenient head-on fashion but not the end user or customers’ need to.
The owner of the dry cleaner mentioned, before I left, that if I was unhappy with the direction of the shirt on the hanger I could always change hangers as many other customers do. Not only do I find it hard to believe that even five percent of any dry cleaner’s customer are taking their shirts off of the wire hangers and putting them on some other sort of customized hanger in their closet, but if I had the time to do that, I’d probably be washing and pressing my own shirts.
The easiest way to microfine this process is clearly for the owner/operator to change the direction of their assembly line from LEFT TO RIGHT to RIGHT TO LEFT. This would ensure everyone in-house and at home had the same advantage of viewing the garments in an advantageous fashion (pun intended).
This change would bear only a nominal expense of moving the machines and stations to the opposite side of the store. Doing this would maintain their current efficiency and likely increase their sales exponentially over time due to the fact that the service they are providing is largely identical to their competitors with one exception…they would have a growing base of customers who, perhaps inexplicably, prefer this dry cleaner over another even though they might not be cognizant as to precisely why. The fact, alone, that it would make a customer’s life even the tiniest bit easier, in my mind, is a strong enough case to change the conventional system this operator employs.
This one man’s kindness in offering me a behind-the-scenes tour of his business, left me with an indelible reminder of the value in consciously considering the lifespan of any product or service beyond the initial point of transaction and the advantage of offering even the subtlest of convenience(s) for one’s customers in a competitive marketplace.
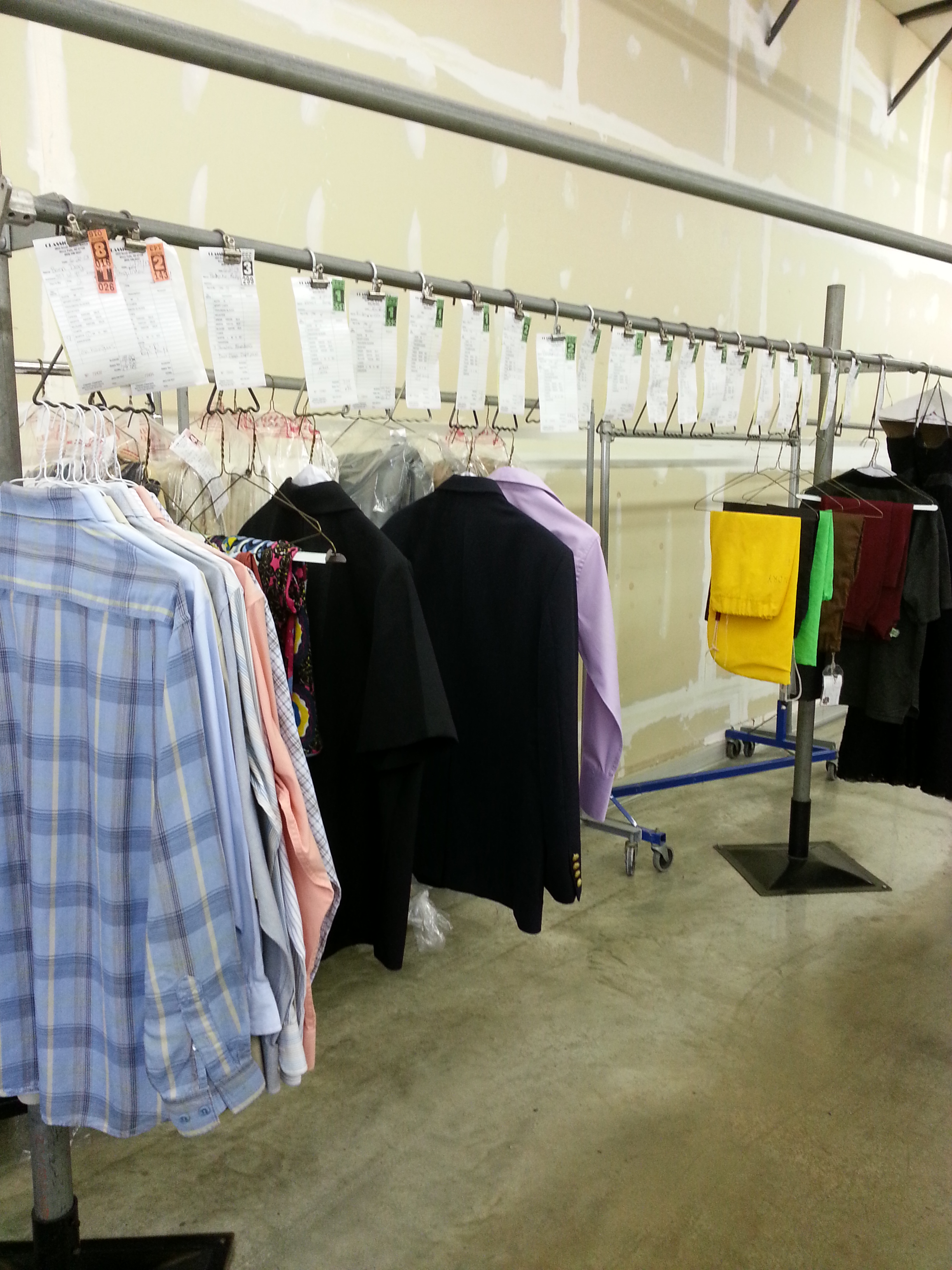
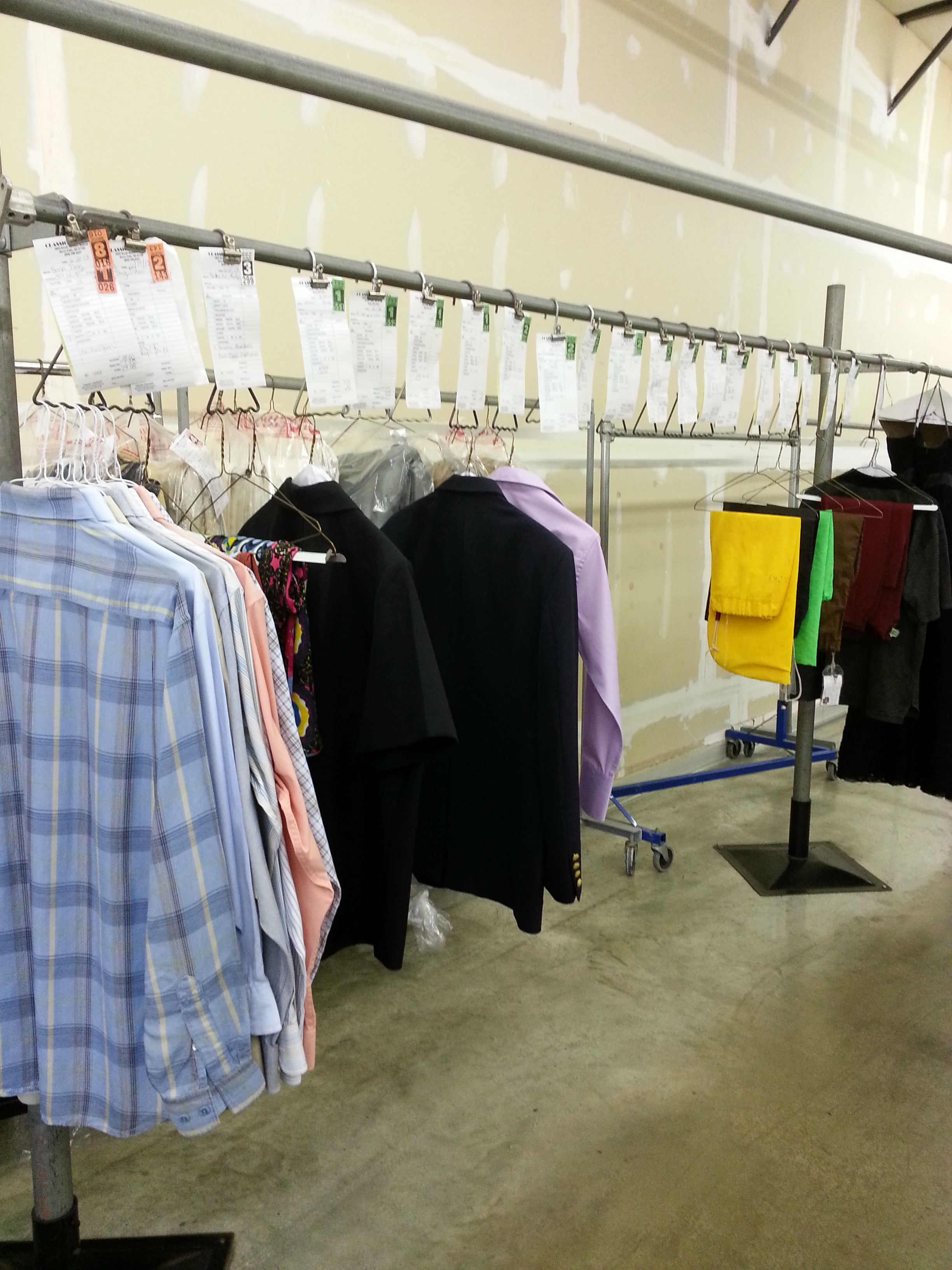
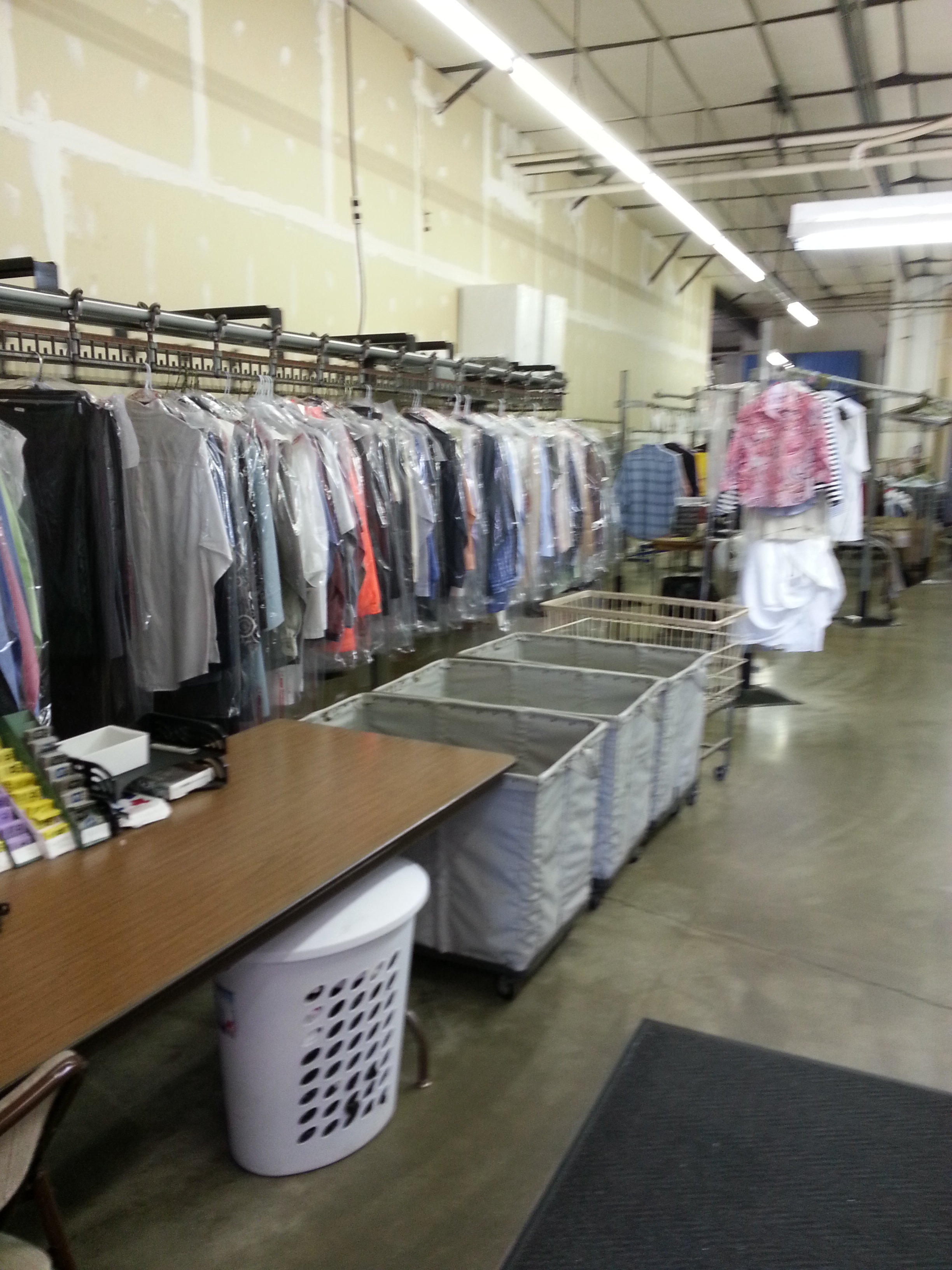
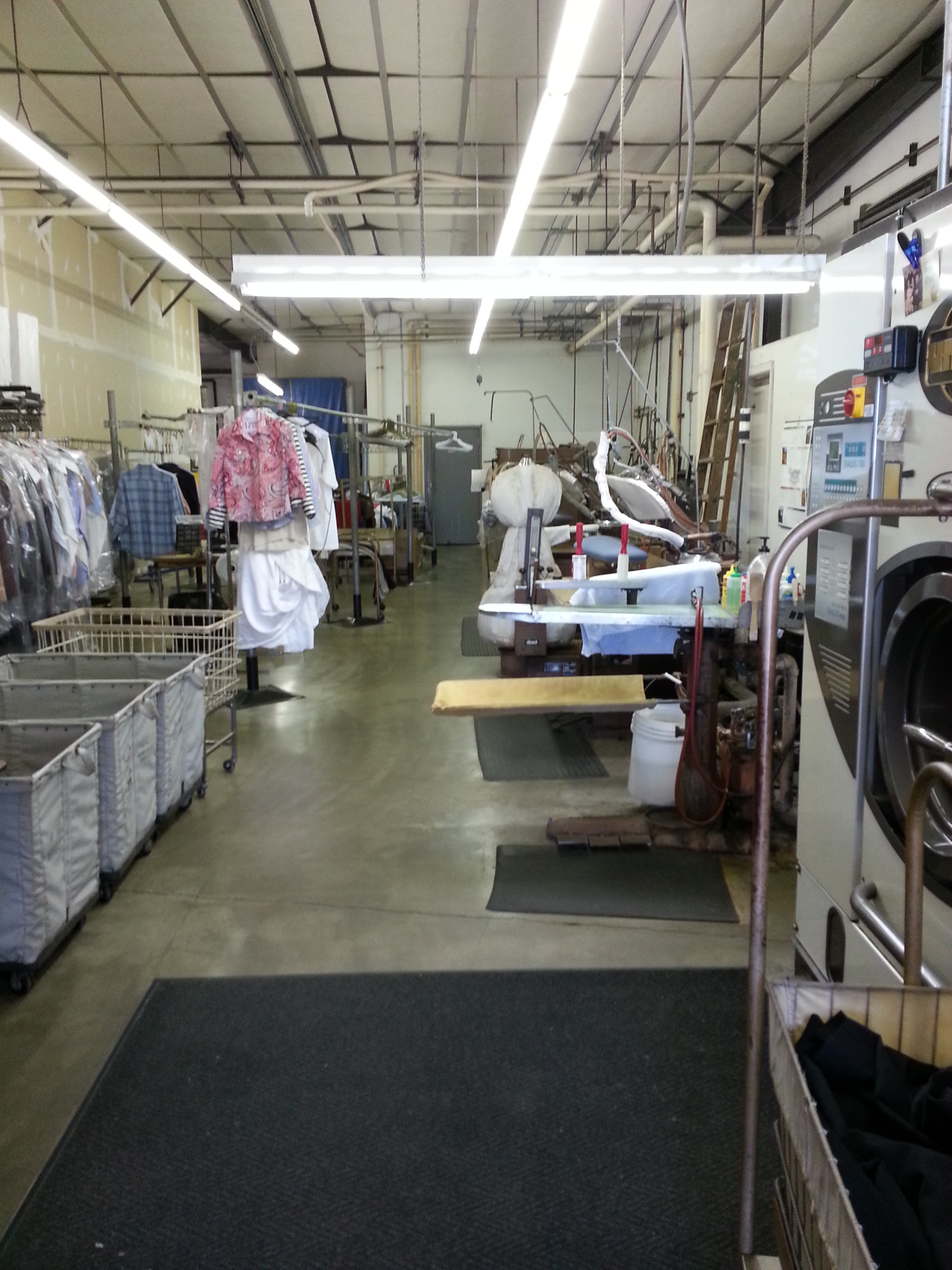
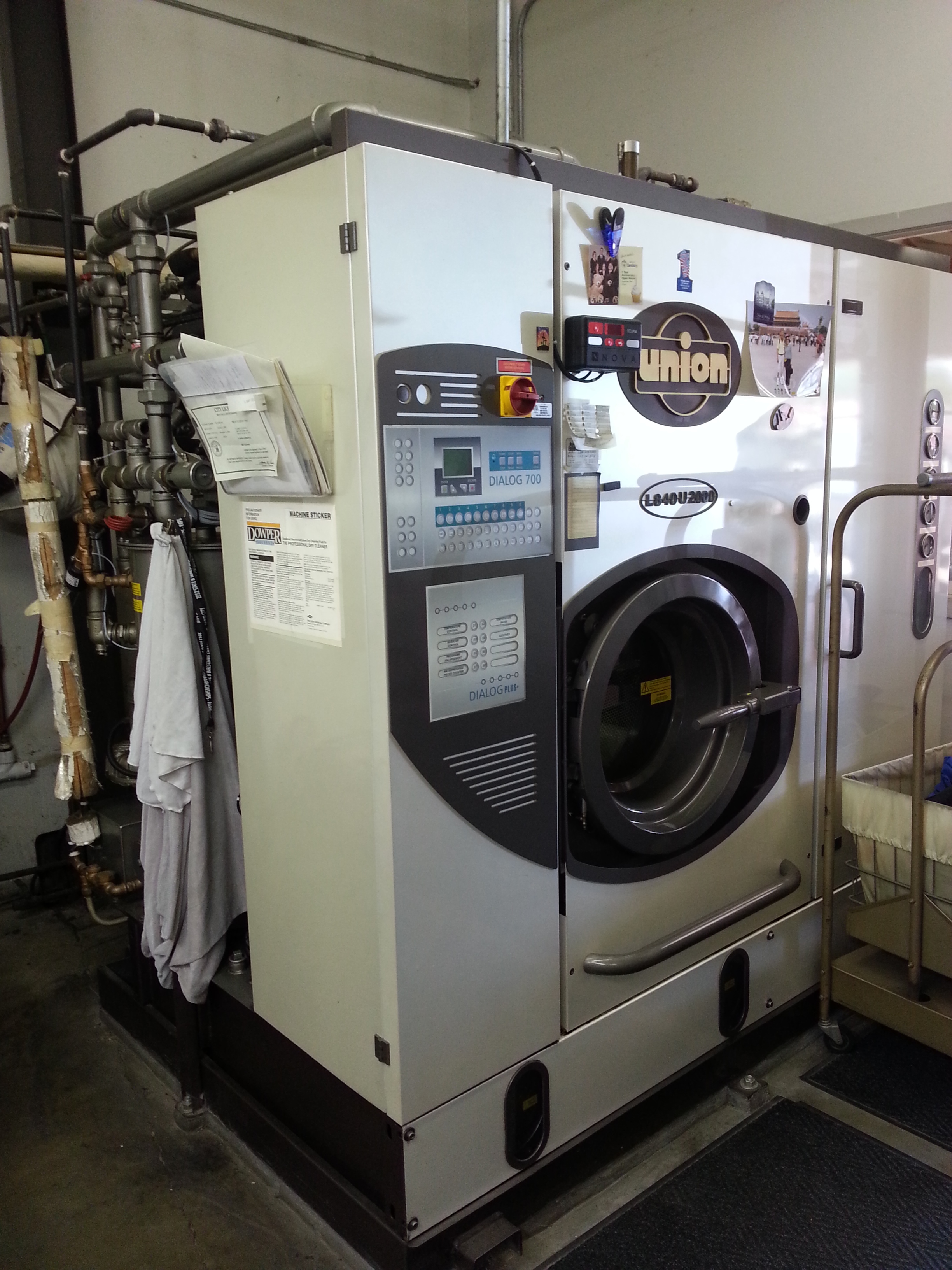
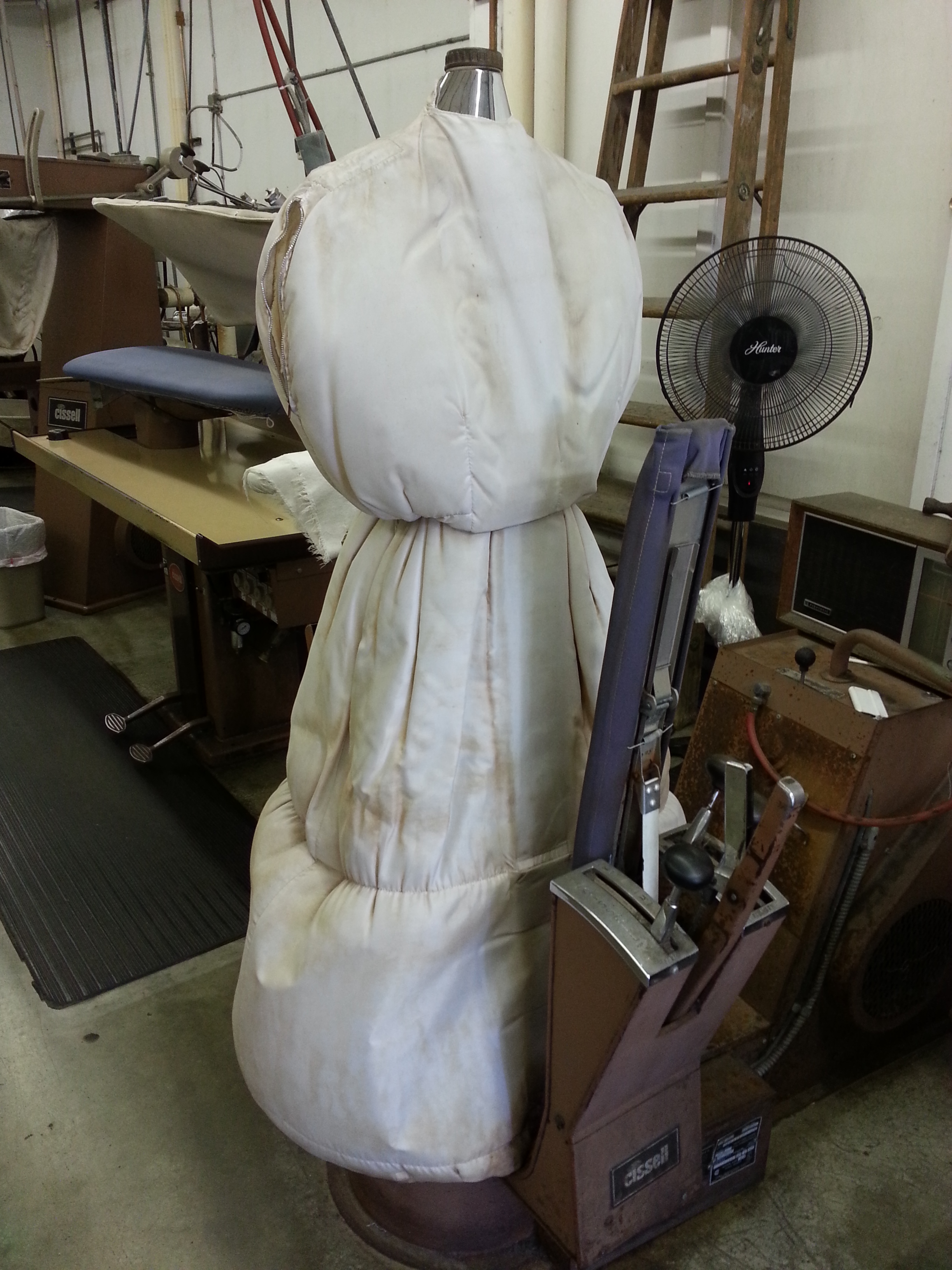
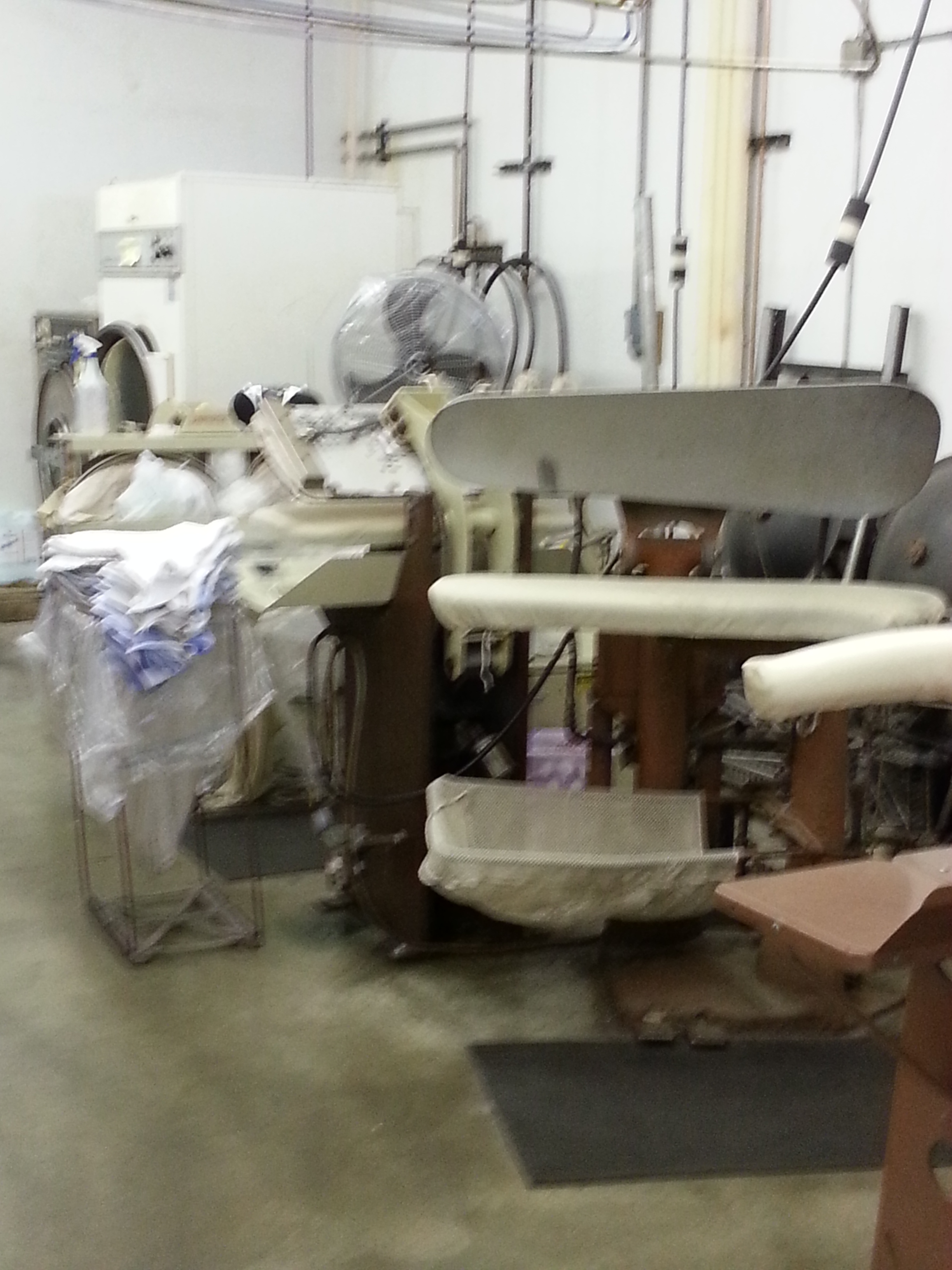
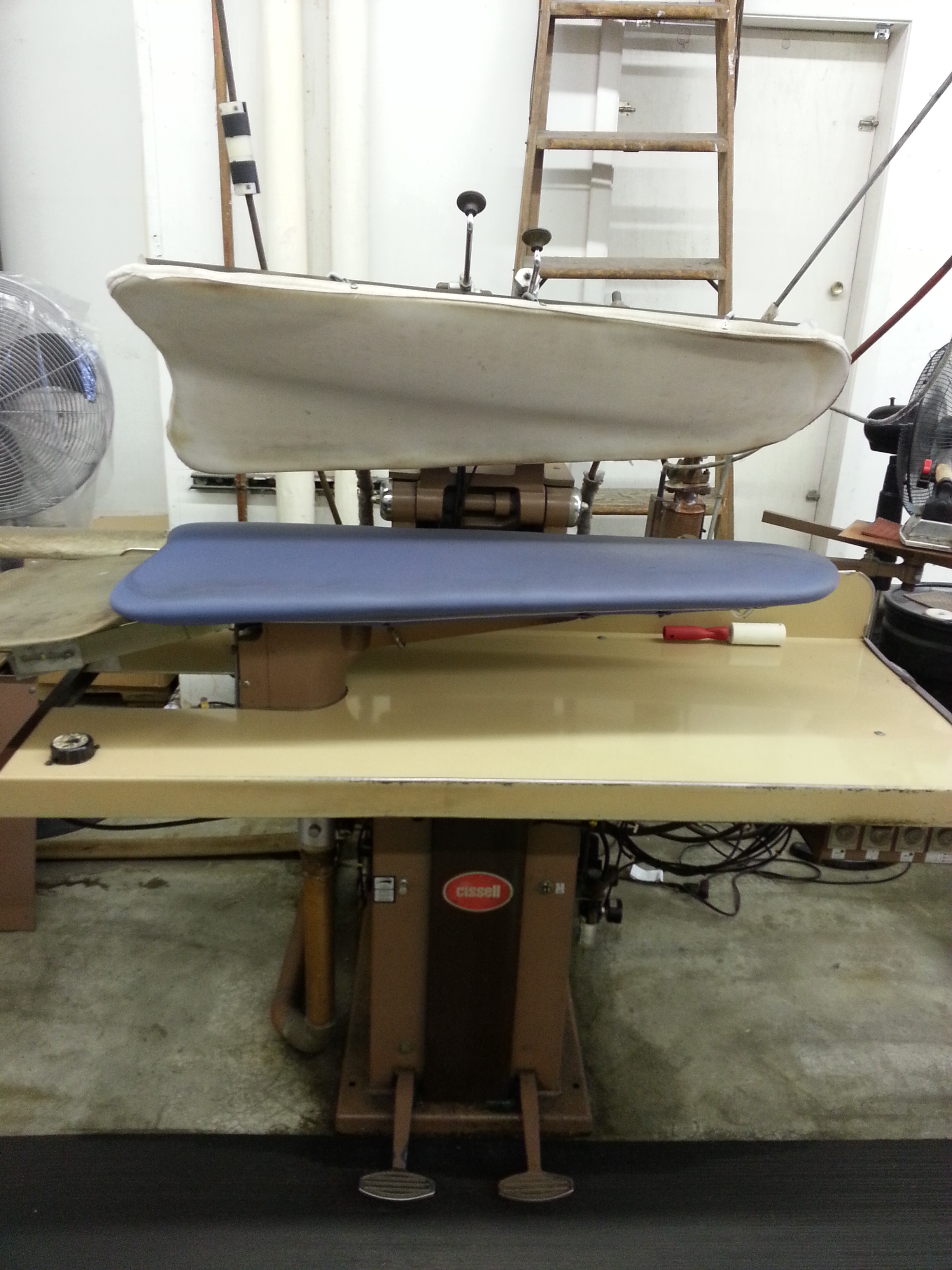
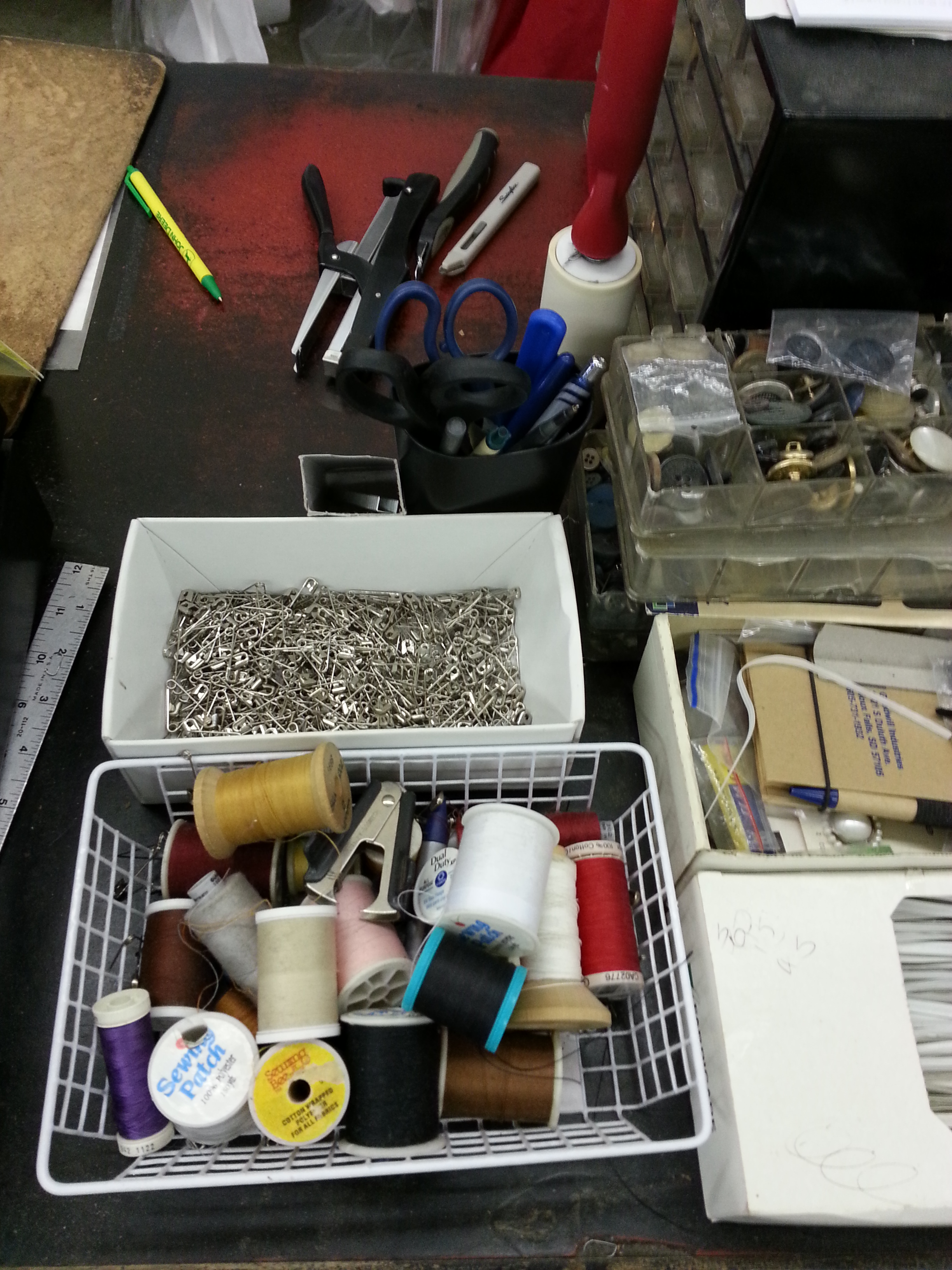
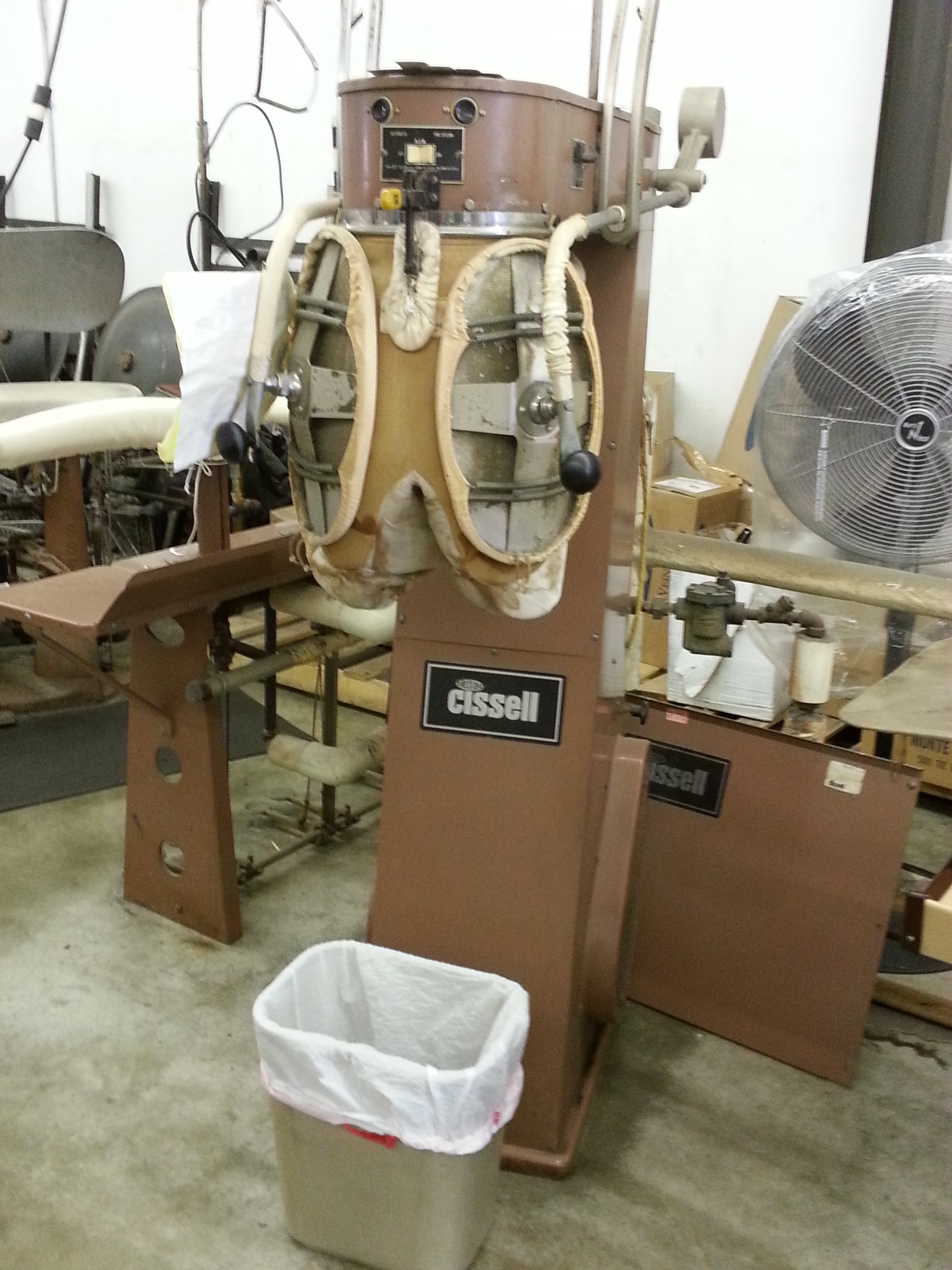
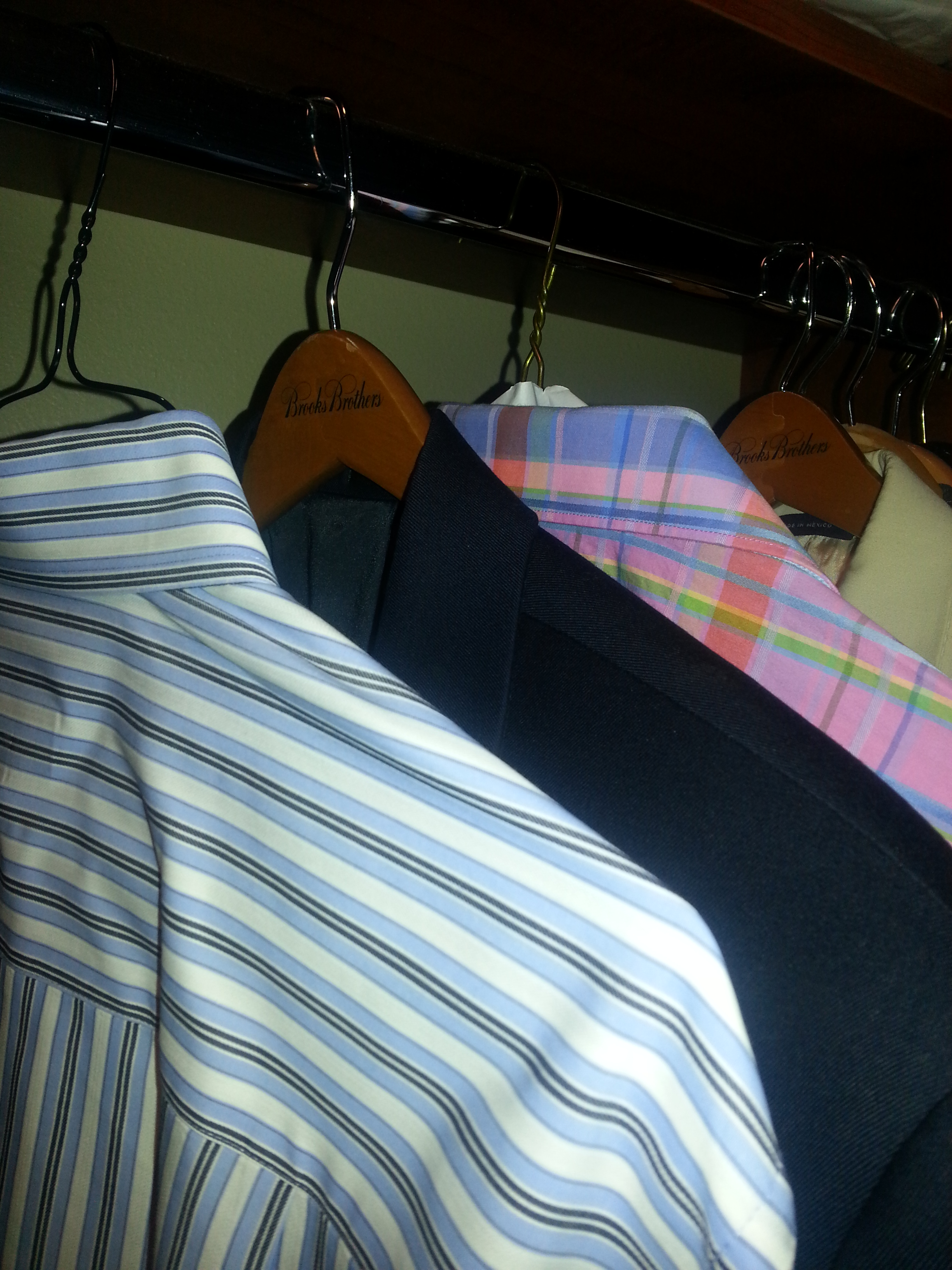